
Welding Symbols
Most of the welding done at Hansen Industries is Microwire (MIG) welding. Tungsten (TIG) welding is a slower process, but in some cases it may be required. If an aluminum part is to have a clear finish, the welds need to be the same colour as the rest of the part. TIG welded joints do not discolour like MIG welded joints.
Typical welding symbols used with sheet metal are shown on a sample part in the diagram. A variety of corners are also shown. These are just a few of the many welding symbols established by the American Welding Society.
To reduce errors we prefer to do our own sheet metal bend calculations. When metal is bent it stretches. The amount the metal stretches is dependent on material type, thickness, bend angle and radius of bend. We draw the part in 3-D CAD software, which automatically unfolds it and gives us a fully dimensioned flat part drawing. This flat layout is then programmed and punched out on one of our CNC turret presses. The flat part is checked against the customer drawing before being deburred and bent.
Tooling charts for both of our CNC turret presses are available upon request.
Welding symbols are a simple way of defining how you want a part welded. You do not have to be a welder to understand the basic principles behind the system. As a designer your concerns are mainly appearance, strength and price. Appearance is important to parts, which are seen by the end user of the product. Smooth corner joints are easier to keep clean and are less likely to rust. To get a smooth rounded corner joint, specify a fully welded and dressed joint. This type of weld is very strong, but expensive because of the labor involved. The cost can be reduced by not specifying a dressed weld, which will sacrifice the appearance somewhat. For lightly loaded parts that do not require aesthetics, a tack weld or stitch weld can be called for. Most welding performed on sheet metal is at the intersection points of two flanges. To join overlapping flanges plug, seam or spot welds are used. Seam and spot welds are best for thin material, although not usually used on aluminum.
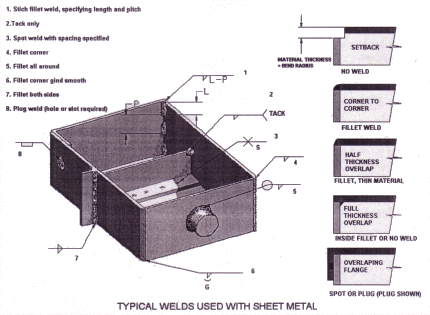